Les fours à induction sont largement utilisés dans les applications industrielles pour le chauffage et la fusion des métaux en raison de leur efficacité, de leur précision et de leur respect de l'environnement.La puissance d'un four à induction est un facteur essentiel qui détermine ses performances, sa capacité et son adéquation à des tâches spécifiques.La puissance nominale des fours à induction varie généralement entre 15 kW et 90 kW pour les modèles compacts, mais elle peut varier en fonction de l'application, du type de matériau et des résultats souhaités.La consommation électrique des fours à induction pour l'acier, par exemple, est d'environ 625 kWh/tonne.Plusieurs facteurs influencent les besoins en énergie, notamment le matériau traité, le temps de chauffage, la productivité, la température et le poids de la pièce.Des caractéristiques avancées telles que la conversion de fréquence IGBT, des systèmes de protection complets et une transmission efficace de la chaleur améliorent encore les performances du four, ce qui en fait un outil polyvalent et fiable pour les processus industriels.
Explication des points clés :
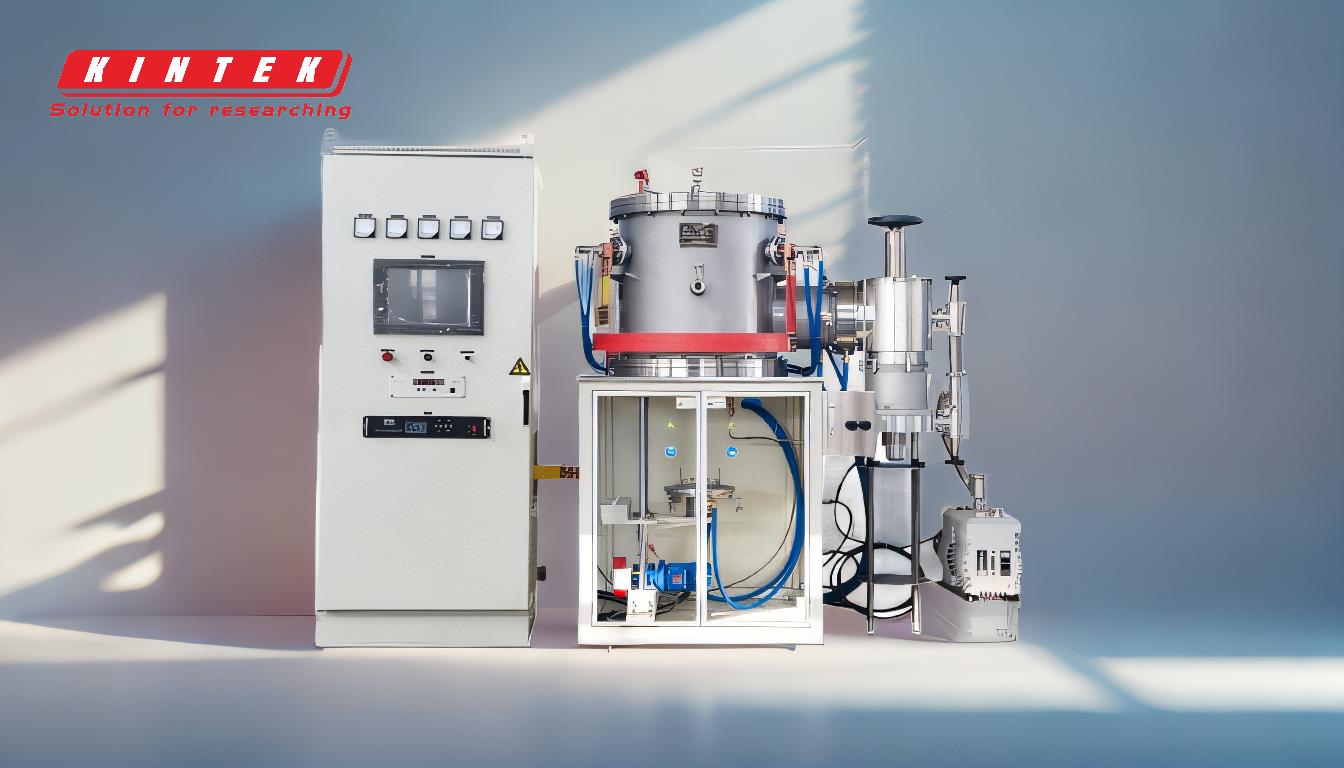
-
Gamme de puissance des fours à induction
- Les fours à induction ont généralement une puissance nominale comprise entre 15 kW à 90 kW pour les modèles compacts.Cette gamme convient aux opérations de petite et moyenne envergure, telles que la fusion de métaux ou le chauffage de pièces.
- La puissance nominale est directement liée à la capacité et à l'efficacité du four.Une puissance plus élevée permet de chauffer et de fondre plus rapidement, ce qui les rend idéaux pour les environnements à forte productivité.
-
Facteurs influençant le calcul de la puissance
-
La puissance requise pour un four à induction dépend de plusieurs facteurs :
- Type de matériau:Les propriétés thermiques des différents matériaux varient, ce qui influe sur l'énergie nécessaire au chauffage ou à la fusion.
- Temps de chauffage:Un chauffage plus rapide nécessite une puissance absorbée plus élevée.
- La productivité:Les opérations à haut débit exigent plus de puissance pour maintenir un rendement constant.
- Température de chauffage:Des températures plus élevées, telles que 1800°C pour la fusion, nécessitent plus de puissance.
- Poids de la pièce:Les pièces plus grandes ou plus lourdes ont besoin de plus d'énergie pour atteindre la température souhaitée.
- Ces facteurs sont basés sur des années d'expérience industrielle afin de garantir des calculs de puissance précis et des performances optimales du four.
-
La puissance requise pour un four à induction dépend de plusieurs facteurs :
-
Consommation électrique standard
- Pour les fours à induction pour l'acier, la consommation électrique standard est de 625 kWh/tonne .Cette mesure fournit une référence pour l'efficacité énergétique et aide à estimer les coûts d'exploitation.
- Les dispositifs d'économie d'énergie, tels que la conversion de fréquence IGBT et les systèmes de contrôle des circuits à puissance constante, contribuent à réduire la consommation d'énergie tout en maintenant une fusion et un chauffage uniformes.
-
Caractéristiques avancées améliorant l'efficacité énergétique
- Conversion de fréquence de l'IGBT:Les fours à induction modernes utilisent la technologie IGBT à l'état solide pour une régulation efficace de la puissance et une conversion de la fréquence.Cela garantit un fonctionnement stable et réduit le gaspillage d'énergie.
- Systèmes de protection complets:Des caractéristiques telles que la protection contre les surintensités, le manque d'eau, la surchauffe, la surtension, le court-circuit et la perte de phase renforcent la sécurité et la fiabilité.
- Transmission de la chaleur et uniformité:Le four assure une bonne transmission de la chaleur et une distribution uniforme de la température, minimisant ainsi les pertes d'énergie et améliorant l'efficacité du processus.
- Agitation magnétique:Le champ magnétique à moyenne fréquence assure un brassage magnétique qui améliore l'uniformité de la composition et l'élimination de l'écume, ce qui accroît encore l'efficacité.
-
Efficacité opérationnelle et flexibilité
- Les fours à induction sont conçus pour une fusion continue 24 heures sur 24 ce qui les rend adaptés aux applications industrielles à forte demande.
- Ils sont légers, mobiles et compacts Les fours de la gamme de produits de l'UE couvrent moins d'un mètre carré, ce qui les rend faciles à intégrer dans les installations existantes.
- Les corps des fours peuvent être facilement remplacés pour s'adapter à des poids, des matériaux et des méthodes de démarrage différents, ce qui offre une grande souplesse pour diverses applications.
-
Capacités de température
- Les fours à induction peuvent atteindre des températures de 1800°C ou plus La température de fusion est de 1800°C ou plus, en fonction du couplage inductif de la bobine avec les matériaux de charge.Ils conviennent donc à la fusion d'un large éventail de métaux, y compris ceux dont le point de fusion est élevé.
- La température de forgeage peut atteindre 1250°C tandis que la température de fusion peut atteindre 1650°C ce qui permet de s'adapter à différents procédés industriels.
-
Efficacité énergétique et avantages environnementaux
- Les fours à induction sont économes en énergie et respectueux de l'environnement réduisant les coûts d'exploitation et minimisant l'impact sur l'environnement.
- Des caractéristiques telles que les systèmes de contrôle des circuits à puissance constante et le balayage automatique des fréquences garantissent un fonctionnement régulier et stable, ce qui améliore encore l'efficacité énergétique.
-
Avantages en matière de conception et de maintenance
- La conception de circuits intégrés de haute qualité simplifie le débogage et le fonctionnement, ce qui rend le four convivial.
- Les composants de l'armoire d'alimentation, tels que les contacteurs CA, les redresseurs commandés au silicium et les cartes d'onduleur, sont bien coordonnés, ce qui garantit une maintenance aisée et une fiabilité à long terme.
-
Considérations spécifiques à l'application
- La configuration de la vitesse de fusion et de la puissance de la taux de fusion et la configuration de la puissance de l'alimentation électrique à moyenne fréquence sont essentiels pour obtenir les résultats souhaités.
- L'utilisation d'une charge propre et une longueur de bloc de four appropriée améliorent l'efficacité, tandis que des matériaux réfractaires appropriés, tels que des creusets en quartz, réduisent la consommation de transfert de chaleur.
En conclusion, la puissance d'un four à induction est un facteur déterminant de ses performances, de son efficacité et de son adéquation à des applications industrielles spécifiques.En comprenant les facteurs qui influencent les exigences en matière de puissance et en tirant parti des fonctions avancées, les utilisateurs peuvent optimiser le fonctionnement du four, réduire les coûts et obtenir des résultats cohérents et de haute qualité.
Tableau récapitulatif :
Aspect clé | Détails |
---|---|
Gamme de puissance | 15 kW à 90 kW pour les modèles compacts |
Consommation d'énergie (acier) | 625 kWh/tonne |
Capacités thermiques | Jusqu'à 1800°C pour la fusion, 1250°C pour le forgeage |
Caractéristiques avancées | Conversion de fréquence IGBT, brassage magnétique, systèmes de protection complets |
Efficacité opérationnelle | Fusion continue 24 heures sur 24, conception légère et compacte |
Efficacité énergétique | Économies d'énergie, respect de l'environnement et réduction des coûts d'exploitation |
Prêt à optimiser votre processus de chauffage industriel ? Contactez nous dès aujourd'hui pour trouver le four à induction idéal pour vos besoins !