Un four de calcination est un four industriel ou de laboratoire spécialisé conçu pour effectuer le processus de calcination, qui consiste à chauffer un matériau à des températures élevées pour chasser l'humidité absorbée, éliminer les constituants volatils comme le dioxyde de carbone et oxyder une partie ou la totalité de la substance.Ce processus est essentiel dans diverses industries, notamment la céramique, la métallurgie et la fabrication de produits chimiques, où un traitement thermique précis est nécessaire pour obtenir les propriétés souhaitées du matériau.Les fours de calcination sont dotés de caractéristiques telles que des capacités à haute température, des commandes programmables et des conceptions écoénergétiques pour garantir des performances et une sécurité optimales.Ils sont utilisés dans des applications allant de la préparation d'échantillons en laboratoire aux procédés industriels à grande échelle.
Explication des points clés :
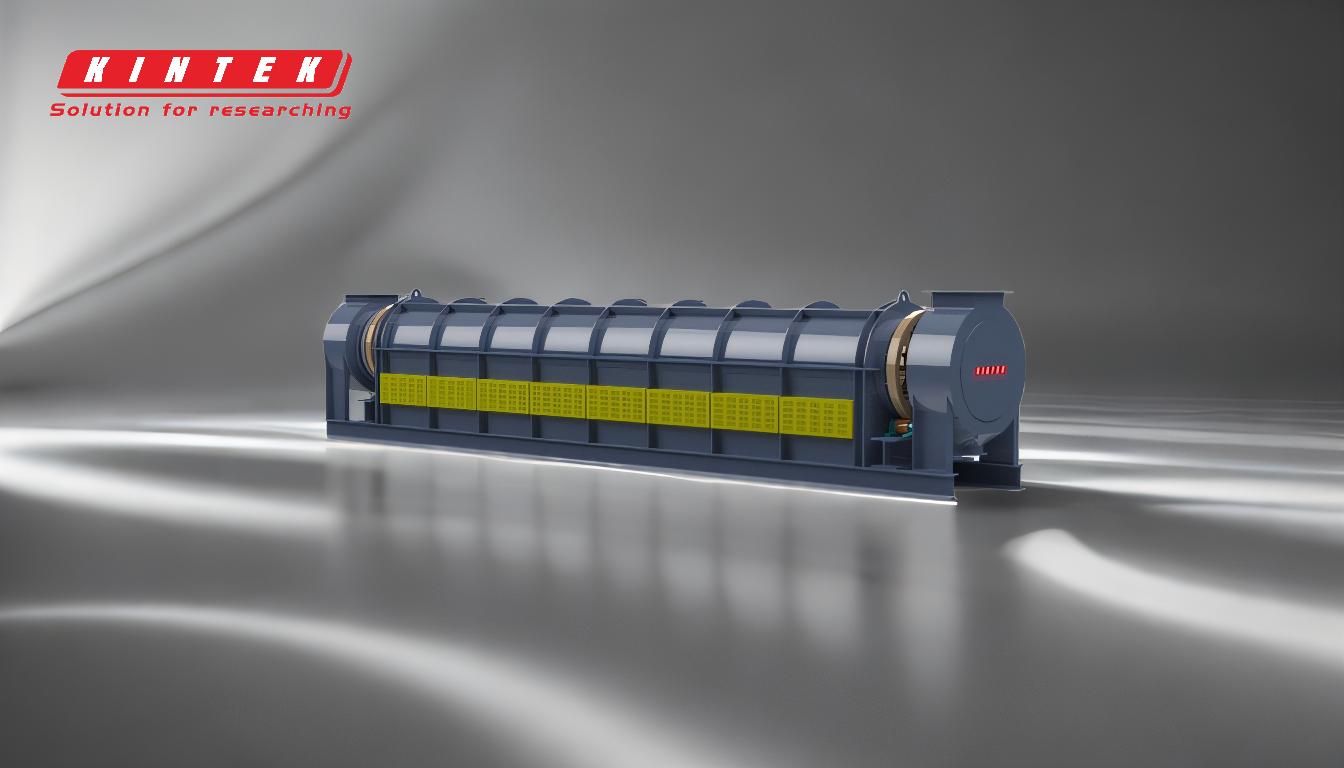
-
Définition et objectif d'un four de calcination:
- Un four de calcination est un dispositif de traitement thermique utilisé pour chauffer des matériaux à des températures élevées en vue de leur calcination.
- La calcination consiste à chasser l'humidité absorbée, à éliminer les constituants volatils (dioxyde de carbone, dioxyde de soufre, etc.) et à oxyder une partie ou la totalité du matériau.
-
Objectifs clés de la calcination:
- Elimination de l'humidité:Élimine l'eau absorbée par le matériau, ce qui est crucial pour les processus nécessitant des matières premières sèches.
- Élimination des constituants volatils:Expulse des gaz comme le dioxyde de carbone ou le dioxyde de soufre, souvent présents dans les matières premières ou formés lors du chauffage.
- Oxydation:Facilite les réactions chimiques qui oxydent le matériau et modifient sa composition et ses propriétés.
-
Applications des fours de calcination:
- Procédés industriels:Utilisé dans les industries telles que la production de ciment, la céramique et la métallurgie pour traiter les matières premières telles que le calcaire, le gypse et les minerais métalliques.
- Utilisation en laboratoire:Employés pour la préparation d'échantillons, les essais de matériaux et la recherche dans des domaines tels que la chimie, la science des matériaux et la géologie.
- Applications environnementales:Utilisés dans le traitement des déchets pour stabiliser ou détoxifier les matières dangereuses.
-
Principales caractéristiques des fours de calcination:
- Capacité à haute température:Conçus pour supporter et maintenir des températures allant jusqu'à 1200°C ou plus, en fonction de l'application.
- Commandes programmables:Equipé de régulateurs PID (Proportionnel-Intégral-Dérivé) et de segments programmables pour une régulation précise de la température et des taux de chauffage.
- Efficacité énergétique:Incorpore des matériaux isolants tels que la fibre céramique ou la fibre d'alumine pour minimiser les pertes de chaleur et réduire la consommation d'énergie.
- Caractéristiques de sécurité:Comprend des enveloppes en acier à double couche, des systèmes de refroidissement par ventilateur et un contrôle de la température pour garantir la sécurité de l'opérateur et la longévité de l'équipement.
-
Types de fours de calcination:
- Fours de laboratoire:Fours cylindriques compacts avec éléments chauffants et isolation intégrés, idéaux pour les expériences à petite échelle et le traitement des échantillons.
- Fours industriels:Conceptions plus grandes et robustes, capables de traiter des matériaux en vrac et de fonctionner en continu, souvent utilisées dans les usines de fabrication et de transformation.
- Fours spécialisés:Adaptés à des applications spécifiques, tels que les fours de combustion pour l'élimination des liants organiques ou les fours de frittage pour la métallurgie des poudres.
-
Considérations relatives à la conception et au fonctionnement:
- Éléments chauffants:Généralement constitué de matériaux tels que le carbure de silicium ou le disiliciure de molybdène, il est disposé de manière à assurer une répartition uniforme de la température.
- Isolation:L'isolation en fibre d'alumine de haute pureté ou en fibre céramique est utilisée pour améliorer l'efficacité thermique et réduire les pertes de chaleur.
- Mobilité et efficacité spatiale:Les modèles de laboratoire sont souvent compacts et équipés de roulettes pour faciliter les déplacements, tandis que les modèles industriels sont stationnaires mais optimisés pour l'utilisation de l'espace.
-
Avantages des fours de calcination:
- Précision:Permet un traitement thermique contrôlé et reproductible, garantissant la constance des propriétés des matériaux.
- Polyvalence:Convient à un large éventail de matériaux et d'applications, de la recherche à petite échelle à la production à grande échelle.
- Efficacité:Une isolation avancée et des commandes programmables minimisent la consommation d'énergie et les coûts d'exploitation.
-
Comparaison avec d'autres chaudières:
- Fours de frittage:Il s'agit de lier des particules à des températures élevées sans les faire fondre, ce qui est souvent utilisé dans la métallurgie des poudres et les céramiques.
- Fours de carbonisation:Conçus pour convertir les matières organiques en carbone par pyrolyse, ils présentent des caractéristiques telles qu'un fonctionnement sans fumée et des taux de carbonisation élevés.
- Fours à haute température:Utilisé pour des processus tels que la fusion et les essais, avec des éléments chauffants sur tous les côtés pour une distribution uniforme de la température.
En résumé, un four de calcination est un outil polyvalent et essentiel pour le traitement thermique, qui permet un contrôle précis des propriétés des matériaux grâce à l'élimination de l'humidité, des composants volatils et de l'oxydation.Sa conception et ses caractéristiques le rendent adapté à un large éventail d'applications, de la recherche en laboratoire à la production industrielle.
Tableau récapitulatif :
Caractéristique principale | Description |
---|---|
Capacité à haute température | Résiste jusqu'à 1200°C ou plus pour les applications exigeantes. |
Contrôles programmables | Les régulateurs PID assurent une régulation précise de la température et des taux de chauffage. |
Efficacité énergétique | L'isolation avancée minimise les pertes de chaleur et réduit la consommation d'énergie. |
Caractéristiques de sécurité | Comprend des boîtiers en acier à double couche, un refroidissement par ventilateur et un contrôle de la température. |
Applications | Utilisé dans la céramique, la métallurgie, la production de ciment et la recherche en laboratoire. |
Types de fours | Fours de laboratoire, industriels et spécialisés pour des procédés spécifiques. |
Améliorez vos capacités de traitement thermique avec un four de calcination. contactez-nous dès aujourd'hui pour obtenir des conseils d'experts !